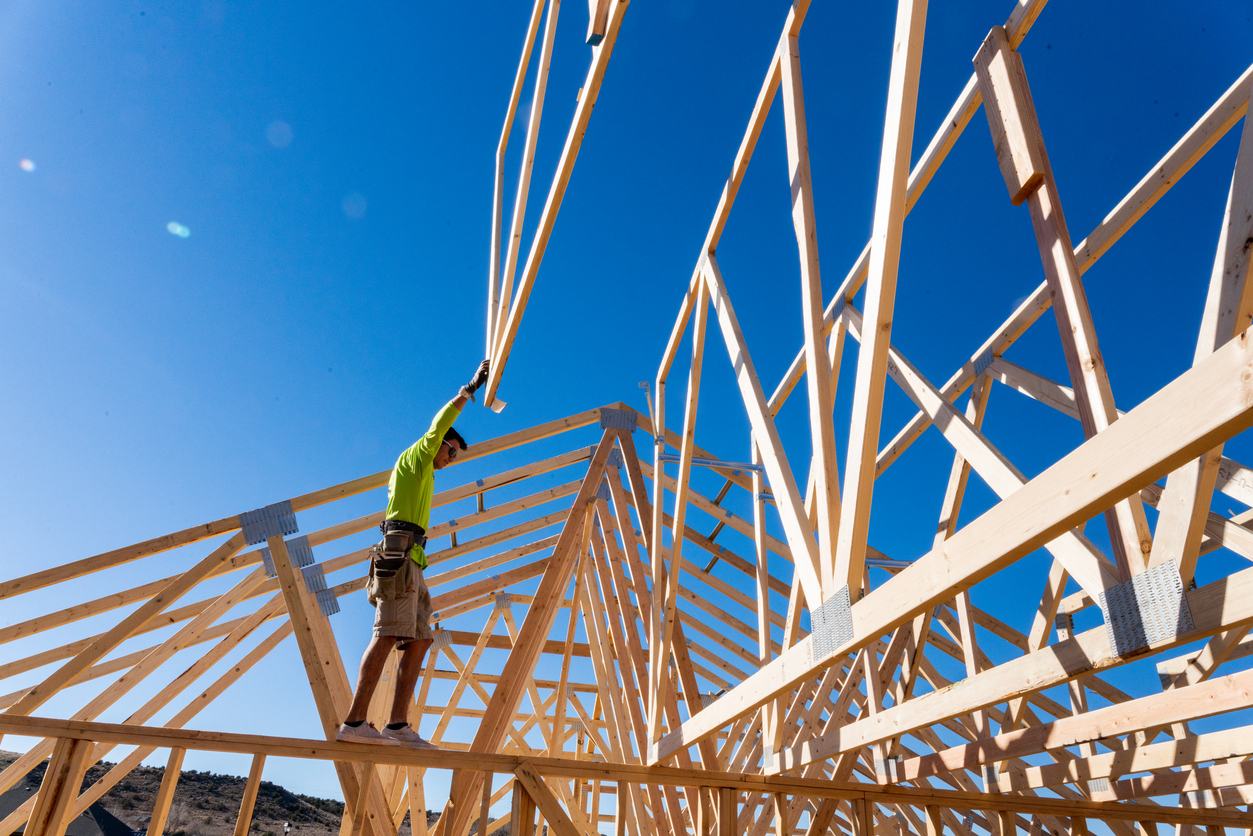
There is more than one way to frame a roof, but which is better? Both have their strengths and drawbacks, and some jobs may even incorporate both methods to construct a roof. Here’s a breakdown of the options.
Stick-Built Roofs
Stick-built roofs consist of rafters—lengths of dimensional lumber cut by carpenters on the jobsite and fastened manually along with a ridge board to form the pitch of a roof.
A stick-built roof consists of the following parts:
Rafters: These create the slope of the roof, and depending on the size and design of the roof are traditionally made from 2x6s, 2x8s, 2x10s and 2x12s. Rafters are fastened to the ridge board at the peak of the roof and at the top plate where they join the wall.
Ridge Beam or Board: lumber installed horizontally to form the peak of the roof.
Ceiling Joist: these form the bottom chord of each rafter and the ceiling for the room below.
Collar Tie: a length of dimensional lumber that connect the rafter on one side of the roof to the corresponding rafter on the opposite side of the roof to prevent the spreading of the rafters.
The Benefits of Stick-Built Roofs
It is easier to transport the roof components than completed trusses. This option is good for remote jobsites or jobsites with limited access for large trucks.
Stick-built roofs are able to be customized and last-minute changes to the design are easily accommodated.
There is less lead time as lumber can be ordered at the same time as the floor and wall framing material and transported to the jobsite.
The Disadvantages of Stick-Built Roofs
All work is conducted onsite so the weather can have a negative impact on progress.
Lumber needs to be properly stored on the jobsite in order to ensure quality.
The quality of the build is determined by the skill of the carpenters, while trusses are factory-built and engineer approved.
Stick framing requires a lot of cutting and hands-on work at roof heights which can pose an increased safety risk.
Stick framing requires site installation of ceiling joists.
The size of the building and the roof pitch may limit the use of stick framing due to the lengths of lumber required.
The cost of labor and lumber is generally higher than it would be with a truss-built roof.
Truss-Built Roofs
Prefabricated trusses are factory built and trucked to the jobsite and lifted into place. Depending on the building size they may be lifted into place by crane. This makes for a time-saving, less material and more economical roof framing option. Trusses are engineered and generally constructed with 2x4s or 2x6s and, because they are machine cut, they are more precisely constructed than those built onsite.
Trusses consist of the following elements:
Top chords (rafter) form the top of the truss.
Bottom chords make up the base.
Web bracing which joins the top and bottom chords and ensures the structural integrity of the truss.
Advantages of Truss-built roofs
Prefabricated trusses are factory made, which makes them more uniform, reliable and precise than those that are hand built. Trusses are manufactured in a controlled environment with high-quality materials. They are manufactured to your building design specifications and are approved by a structural engineer.
Roof assembles go up quicker so you save time and aren’t affected as much by inclement weather.
Less time on scaffolding and ladders make for a safer jobsite.
Trusses are generally cheaper than stick-built assemblies.
Trusses use up to 25% less lumber and creates less jobsite waste than stick-built roofs.
Disadvantages of Truss-built roofs
Due to their weight, trusses need to be transported by truck and depending on the size of the building may be placed by crane. In remote areas and in areas with limited access like narrow streets, truss delivery and installation may not be possible.
Prefabrication means that no last-minute changes are possible and it limits your roof design potential.
Unless there is a specific requirement or request at the time the trusses are ordered attic spaces are limited with truss designs.
Because trusses are build for a specific building the truss manufacturer may in some cases want to take measurements at the top plate to ensure the trusses are built correctly for that structure.